Reports from the field and for the field
Developing innovative software like ADVISIM3D is like having a crazy idea and having it tamed and nurtured by caring software engineers. But no matter how well you nurture it, there comes a time when it has to be released into the wild. Since 2021, ADVISIM3D has had to find its way in the practice of industrial spray cleaning processes, survive, convince natural skeptics, arouse the curiosity of potential customers and ultimately win them over. We will keep you up to date on the progress here.
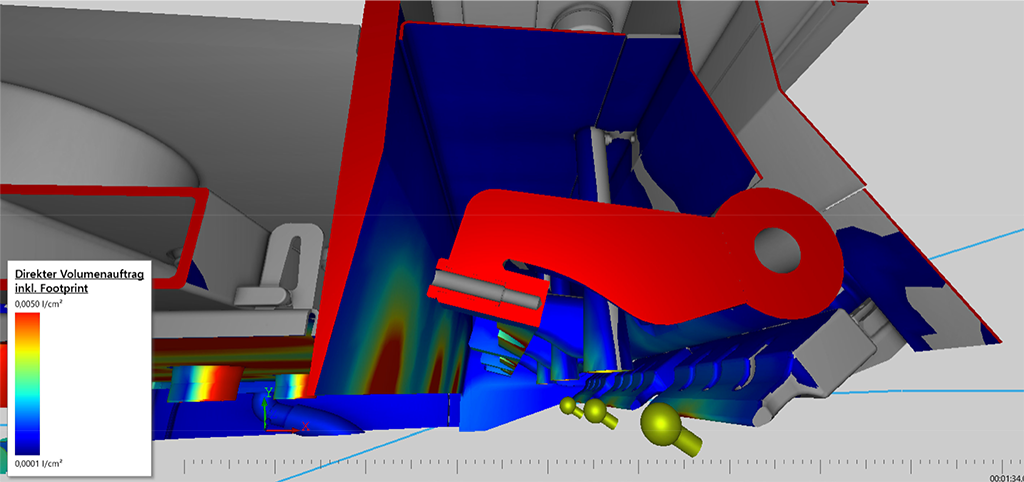
To optimize its machine development, SIG, a company with around 9,000 employees and an annual turnover of 3.2 billion euros, has been relying on the standard software ADVISIM3D for the packaging industry and plant engineering from the Saxon software company ADVITEC Informatik GmbH since 2021.
The goal
Carton packaging must keep fruit juices or coconut milk unrefrigerated, food-safe and product-stable for many months at an average temperature of 30 degrees, even under the most demanding climatic conditions, such as in the North Moluccas.
SIG has developed its aseptic filling technology for this purpose. It offers maximum food safety and quality with a shelf life of up to 12 months. There is no need for energy-intensive cooling or the use of preservatives.
New systems or prototypes must be commissioned and validated on site at the customer's premises. As R&D employees from Linnich, for example, the German development and production site, have to fly long distances and often change planes before they arrive at a customer in Brazil, for example, variants and operating scenarios are examined as early as possible in the development process.
The challenge
Aseptic filling and packaging machines place the highest demands on the cleanability of all lines and surfaces that come into contact with food. This is why the entire development process of such a high-tech system follows the requirements of hygienic design. Nevertheless, for a long time, even those systems that have to fill absolutely sterile products were cleaned manually using CIP (cleaning in place) systems for rinsing the pipes.
The solution
Modern machines are characterized by an increasing proportion of automatic cleaning processes.Various nozzle types such as rotating nozzles, flat jet nozzles or full cone nozzles are used. SIG uses the latest digital methods in addition to testing when designing and configuring these sophisticated processes.ADVISIM3D was used for the first time at SIG for the fundamental redevelopment of an aseptic filling machine and helped with the selection and positioning of the nozzles.
The machine's sterile chamber to be cleaned has a complex structure and features many internals, undercuts and spray shadows. ADVISIM3D enabled the engineers to virtually simulate the cleaning effect of different nozzle types and arrangements and thus find the optimum configuration quickly, easily, cost-effectively and, above all, in accordance with the hygienic design specifications.
Advantages of simulation
Simulation allows the cleaning process to be optimized in the development phase before the machine is physically built. This saves time and costs, as costly modifications to the real machine can be avoided. The simulation makes it possible to reduce the number of nozzles required and at the same time ensure effective cleaning. Potential weak points in the cleaning design can thus be identified and rectified at an early stage.
Validation of the simulation
The simulation results were partially validated by tests on real assemblies.This showed that the simulation reproduced reality well in the vast majority of cases.For the few deviations, e.g. in the simulation of draining water, the engineers' experience is used to realistically interpret and adapt the simulation results.
Summary
The use of ADVISIM3D has helped SIG to make the cleaning processes in new aseptic filling machines more efficient and effective. The simulation software makes it possible to speed up the development process, reduce costs and no longer oversize cleaning processes for safety reasons.
SIG uses ADVISIM3D as a digital assistant in addition to the experience of the engineers, because simulation does not always perfectly reflect reality.
By combining simulation and real-life testing, SIG can ensure that its state-of-the-art aseptic filling machines with fully automated cleaning meet the high standards of cleanliness and sterility required - worldwide, even in the most remote locations such as the North Moluccas.
___________________________________________________________________________________________
⭸ twitter.com/ADVITEC
⭸ twitter.com/advisim3
⭸ ADVITEC bei Linkedin
⭸ ADVITEC bei XING
Hygiene meets high-tech: SIG relies on ADVISIM3D for global food safety
North Moluccas, ever heard of it? And what does this northern Indonesian diver's paradise have to do with the ADVISIM3D virtual simulation software for industrial spray cleaning processes? Well, even in this exotic location, state-of-the-art packaging machines from SIG demonstrate their superior technological expertise for the hygienic, aseptic filling of food products.
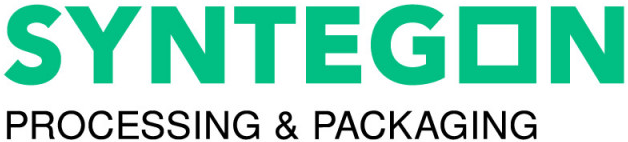
ADVISIM3D optimises container interiour cleaning at Pharmatec GmbH, a Syntegon Company
In the manufacture of pharmaceuticals, customers of Dresden-based Pharmatec place high demands on the quality of the cleaning of containers and production facilities. In modern plants, production residues are removed using automated cleaning systems. A particular problem arises with containers with large volumes and diverse or complicated internals.
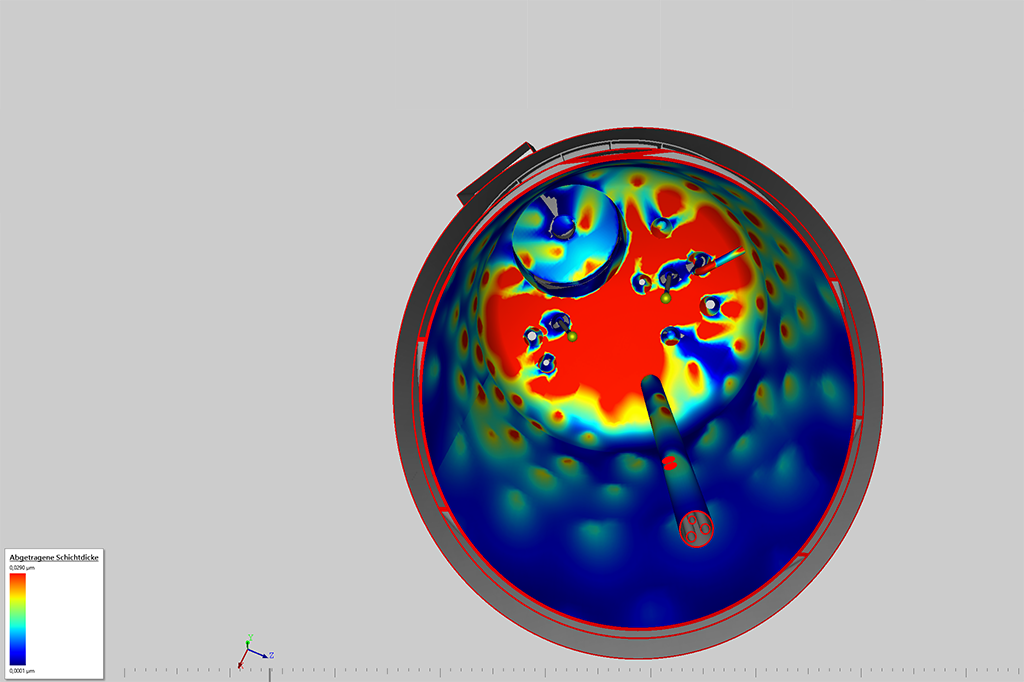
Pharmatec, a Syntegon Group company based in Dresden, Germany, offers complete solutions for the production, distribution and storage of high-purity media such as HP, HPW, PS and WFI. In addition, pharmaceutical manufacturers receive modern formulation systems for large and small-volume parenterals as well as tried and tested, practice-orientated bioprocess systems and services including future-proof automation solutions. The focus is on hygienic and sterile processes for pharmaceuticals, biotechnology, cosmetics and other good manufacturing practice industries in quality assurance.
The challenge
In the production of pharmaceuticals, our customers place high demands on the quality of the cleaning of containers and production facilities.
In modern systems, production residues are removed using automated cleaning systems. A particular problem arises with large-volume containers and diverse or complicated installations. Here, agitator parts, inlet pipes or measuring technology can protrude into the tank interior. These installations form spray shadows and hinder the cleaning of product residues by spray balls or cleaning nozzles installed in the tank.
However, the optimum positioning of the spray balls in the container is crucial for the quality and efficiency of the cleaning process. Until now, this task has been performed on the basis of empirical values and, in cases of doubt, with complex test trials. This is resource-intensive and often leads to oversized systems in order to guarantee reproducible cleaning success.
Solution with ADVISIM3D
Pharmatec uses the 3D cleaning simulation software ADVISIM3D from ADVITEC to optimise the planning and validation of CIP cleaning processes. The software enables the virtual simulation of spray cleaning processes, the analysis of spray shadows, volume flow distribution and cleaning effect.
Advantages and benefits
• Time and cost savings:
The virtual simulation allows different nozzle configurations and cleaning parameters to be tested quickly and easily without having to carry out complex analogue tests. This significantly reduces the time required for the design, dimensioning and validation of cleaning systems.
• Conservation of resources:
Avoiding spray shadows and oversizing through optimised nozzle configurations leads to lower consumption of cleaning media, water and energy.
• Better cleaning results:
The ability to virtually test a variety of configurations allows Pharmatec to find the optimal balance between effort and benefit in achieving the cleaning goal.
• Transparent documentation:
ADVISIM3D enables the creation of meaningful documentation. The simulation results can be output as colour visualisations and reports and stored in the technical documentation for cleaning planning.
Cooperation with ADVITEC
Pharmatec was already involved as a competence partner in the SIMKOR research project, which served as the basis for the development of ADVISIM3D. Pharmatec's practical tests under real-life conditions provided valuable insights for the development of a meaningful cleaning simulation.
Conclusion
The use of ADVISIM3D enables Pharmatec to design cleaning processes for internal container cleaning for customers in the pharmaceutical industry in a more efficient and resource-saving manner. The simulation can save time and costs right from the planning phase, improve cleaning quality and at the same time fulfil the strict requirements of the pharmaceutical industry.
"ADVISIM3D sets an unrevalled standard in the simulation of container interior cleaning. The 3D visualization and user-friendliness are impressive and the results are precise and save costs for expensive test series and conversions." Torsten Große - Design Manager | Standardization and Design Requirements (PADD/ENG-N) | Syntegon Technology GmbH
Are you interested in whether cleaning simulation with ADVISIM3D could also be suitable for your application? We would be happy to talk about it, personally introduce you to ADVISIM3D and answer all your questions. Give us a call and make an appointment on +49 351 6526222 or use the form
___________________________________________________________________________________________
⭸ twitter.com/ADVITEC
⭸ twitter.com/advisim3
⭸ ADVITEC bei Linkedin
⭸ ADVITEC bei XING
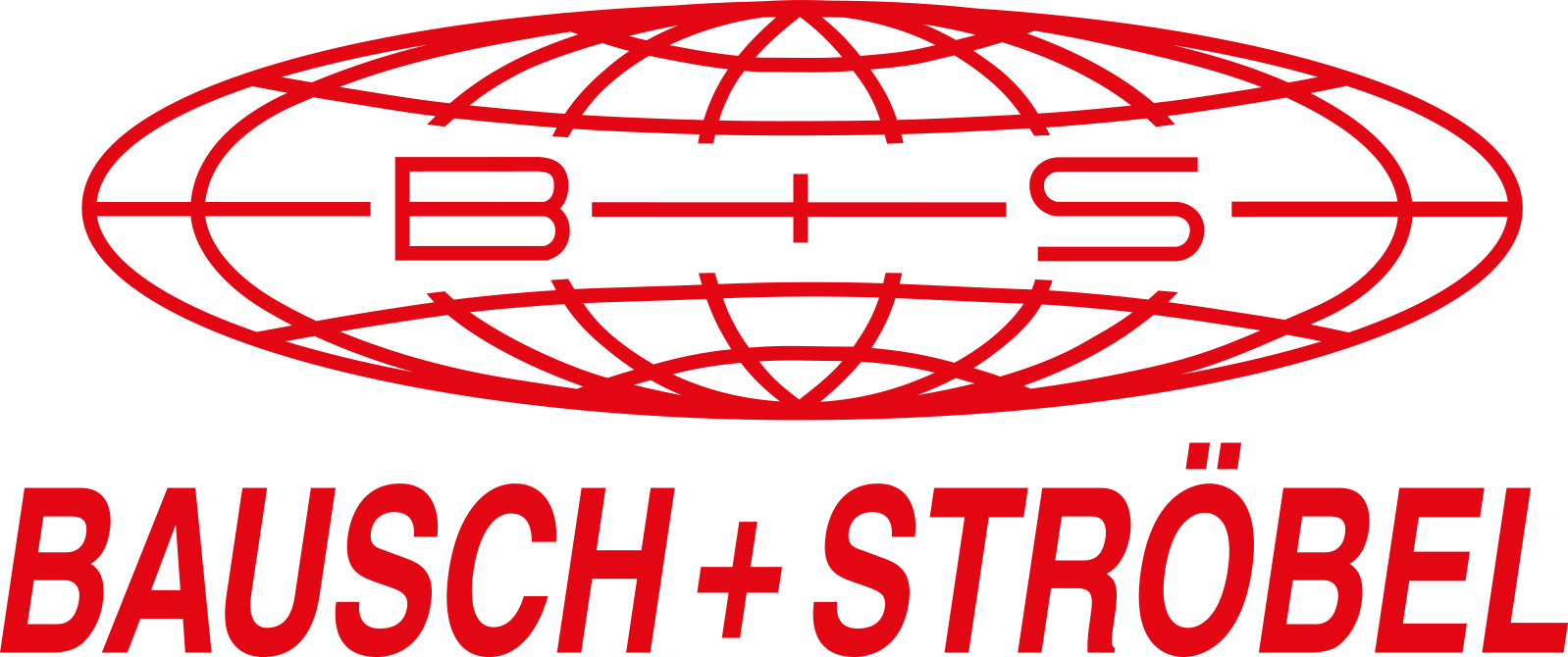
ADVISIM3D revolutionises bottle cleaning in pharmaceutical filling and packaging technology at Bausch+Ströbel SE Co. KG
High demands are placed on the cleaning of pharmaceutical machines and containers. For example, bottles for storing and transporting vaccines must be cleaned hygienically before filling in order to reliably remove possible contamination from production, packaging or transportation. A second cleaning process concludes production in order to remove any residue from the outside of the bottles and make the containers ready for transportation.
Bausch + Ströbel, a leading global provider of pharmaceutical packaging solutions with almost 60 years of company history and numerous awards, relies on the virtual cleaning simulation ADVISIM3D. In its own approach, the company uses the software, which is usually used for the internal cleaning of containers, to successfully simulate and optimize the external cleaning of bottles virtually.
The challenge
The bottles are held in place by machine clamps and guided past the cleaning nozzles - static full-cone nozzles at the top and vertically movable flat ejectors at the bottom. WFI water (Water For Injection) is used as the cleaning fluid and compressed air is used for drying. The machine clamps cast spray shadows, making cleaning more difficult. WFI is also comparatively expensive.
The target for optimizing the positioning of the nozzles and clamps using the ADVISIM3D virtual cleaning simulation is a 50 percent saving in WFI, which in this case corresponds to around 250 l/h. In addition, the number of time-consuming cleaning cycles is to be reduced. In addition, the number of time-consuming and cost-intensive analog cleaning tests with riboflavin or diatomaceous earth corn starch should also be halved as far as possible.
The solution
With ADVISIM3D, any number of scenarios can be simulated virtually, without physical prototypes or complex test setups. Different new nozzles, bottle sizes and bottle quantities as well as nozzle positioning and gripper arrangements are simulated. The results of the simulations with direct volume flow application and removed layer thicknesses between 30 and 55 µm match the photo-documented results of the analog tests.
The advantages
The virtual optimization of external bottle cleaning with ADVISIM3D delivers convincing results. Weak points in the cleaning process, such as areas covered by the holding clamps that are difficult to clean, are identified and eliminated. By making targeted adjustments to the nozzle positions and the mounting of the holding clamps, e.g. smaller mounting surfaces, larger distances and modified holding positions, Bausch + Ströbel can continuously improve the cleaning performance and at the same time reduce the consumption of expensive WFI water. The number of physical test runs required is actually halved from 5-6 to 2-4, which saves a lot of time and money.
Prospects
The successful use of ADVISIM3D outside of the usual application scenarios in container interior cleaning demonstrates the flexibility and enormous potential of this innovative virtualization software. Bausch + Ströbel is also planning to use ADVISIM3D for the cleaning simulation of machine surfaces and for large CAD models with more than 10,000 components, underlining its confidence in the software as a reliable digital assistant and an innovative and efficient virtualization solution in pharmaceutical filling and packaging technology.
Are you interested in whether cleaning simulation with ADVISIM3D could also be suitable for your application? We would be happy to talk about it, personally introduce you to ADVISIM3D and answer all your questions. Give us a call and make an appointment on +49 351 6526222 or use the form
___________________________________________________________________________________________
⭸ twitter.com/ADVITEC
⭸ twitter.com/advisim3
⭸ ADVITEC bei Linkedin
⭸ ADVITEC bei XING

ADVITEC Manufacturer Report | Why we developed ADVISIM3D and brought it to market maturity
ADVISIM3D is the market-leading digital answer to the current analog challenges of hygiene safety, resource and environmental protection in industrial cleaning. Together with our cooperation partners in the publicly funded SIMKOR research project, we recognized the need for a virtualization solution for the planning, validation and optimization of spray cleaning processes at an early stage. Conventional methods based on analog tests were time-consuming and resource-intensive and often led to oversized cleaning systems for safety reasons.
Together with our cooperation partners in the publicly funded SIMKOR research project, we recognized the need for a virtualization solution for the planning, validation and optimization of spray cleaning processes at an early stage. Conventional methods based on analog tests were time-consuming and resource-intensive and often led to oversized cleaning systems for safety reasons.
As a leading research institute in the field of static and dynamic spray cleaning, the Fraunhofer Institute for Process Engineering and Packaging (IVV) Dresden was an important initial source of inspiration. The institute has many years of experience in cleaning technology, particularly in the experimental research of interactions and in the monitoring and recording of cleaning processes. As part of SIMKOR, the Fraunhofer IVV Dresden was responsible for collecting the metrological data. Comparable data also form the physical basis for reliable and realistic predictions of the cleaning effect of ADVISIM3D.
Since its market launch in 2021, ADVISIM3D has been continuously developed and improved to meet the requirements of users in the field and to establish the software as the industry standard for the pharmaceutical, food, manufacturing and other sectors.
Arguments in favor of the ADVISIM3D virtual cleaning simulation
- Resource efficiency: ADVISIM3D can be used to virtually simulate and optimize cleaning processes in order to reduce the consumption of cleaning fluids, water and energy.
- Accuracy and reliability: The software is based on scientific data and algorithms provided by the Fraunhofer IVV Dresden as part of the SIMKOR project, enabling precise simulations and valid statements about the cleaning effect.
- Time and cost savings: ADVISIM3D accelerates the design and validation process of cleaning systems, reduces the need for time-consuming analogue tests and minimizes downtimes.
- Improved transparency and documentation: The software provides a 3D visualization of the cleaning process and enables automated reporting. This increases transparency and simplifies documentation.
- Continuous innovation: ADVITEC regularly optimizes and updates ADVISIM3D to meet the changing requirements of the industry and to integrate new functions.
Conclusion
"ADVISIM3D is the first market-ready product of our strategic development offensive 'Software for industrial cleaning'. Since 2015, ADVITEC has been building up in-depth expertise in the digitalization of cleaning processes, particularly in the areas of virtual simulation and robot control. We regularly contribute our expertise to research and funding projects with partners from science, industry and politics. Our common goal: resource optimization through more efficient cleaning processes for the benefit of the environment, society and companies."
Norbert Ebersbach - Managing Director and Product Manager | Project ADVISIM3D | ADVITEC Informatik GmbH
___________________________________________________________________________________________
⭸ twitter.com/ADVITEC
⭸ twitter.com/advisim3
⭸ ADVITEC bei Linkedin
⭸ ADVITEC bei XING